フュームドシリカ(Fumed Silica、微粒子シリカ)は、1942年にカーボンブラックの代替品としてドイツDegussa社(現・Evonik Industries社)の化学技術者H. Kloepferによって開発され、煙のような外観からフュームドシリカと呼ばれています。
また、合成法から乾式シリカや火炎加水分解法シリカとも呼ばれ、外観は白色粉末です(Photo1)。 フュームドシリカは、液体の増粘・チキソトロピー性付与、粉体の流動性改善、エラストマーの補強などの機能を持ち、塗料、印刷インキ、接着剤、プリンタートナー、ゴムなど幅広い分野で利用されています。
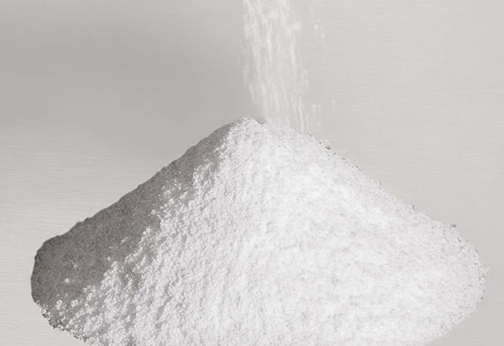
Photo1. 粉末シリカの外観
フュームドシリカは、非晶質シリカのなかまです。シリカゲルや沈降性シリカのように製造に水を用いる方(湿式法)で製造されるため、湿式シリカとも呼ばれています。一方、フュームドシリカは、水を使用しない方法(乾式法)で製造されるため、別名『乾式シリカ』とも呼ばれています(fig1)。
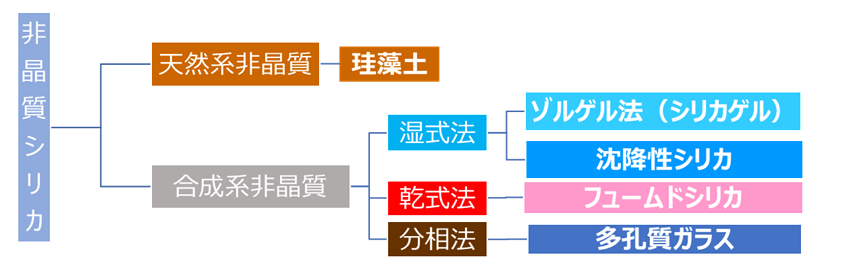
Fig1. 非晶質シリカの分類
粒子構造
フュームドシリカの粒子は、シリカゲルや沈降性シリカのような湿式シリカと同様に脱水縮合により一次粒子径が形成され、その一次粒子をベースに二次粒子が形成されますが、大きく異なる点は、四塩化ケイ素が用いられている点です。
素が用いられている点です。また、沈降性シリカやシリカゲルに比べて一次粒子により構成される粒子(二次粒子)が小さいのが、フュームドシリカの大きな特徴です。
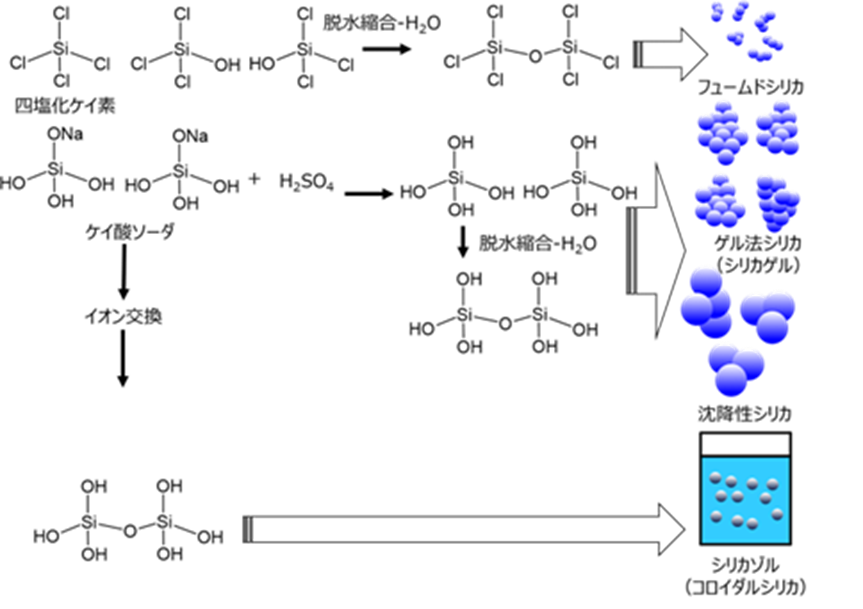
Fig2. 非晶質合成シリカの二次粒子形成イメージ
一次粒子から二次粒子への成長
一次粒子から二次粒子が形される過程には、pHと塩が非常に重要です。
一次粒子が形成される際に、pHが低く(酸性側)かつ、塩が多量の存在する場合には、一次粒子が成長せずに、直径が数ナノ程度で小さいまま二次粒子形成します。一方、pHが高く、塩が少ないほど一次粒子が成長して、二次粒子を形成します。
フュームドシリカは、Fig3の赤いアンダーラインで囲った領域で粒子成長が行なわれ、赤丸の部分が二次粒子になります。このようにフュームドシリカは、比較的一次粒子が小さいため、それによって形成される二次粒子も小さくなります。
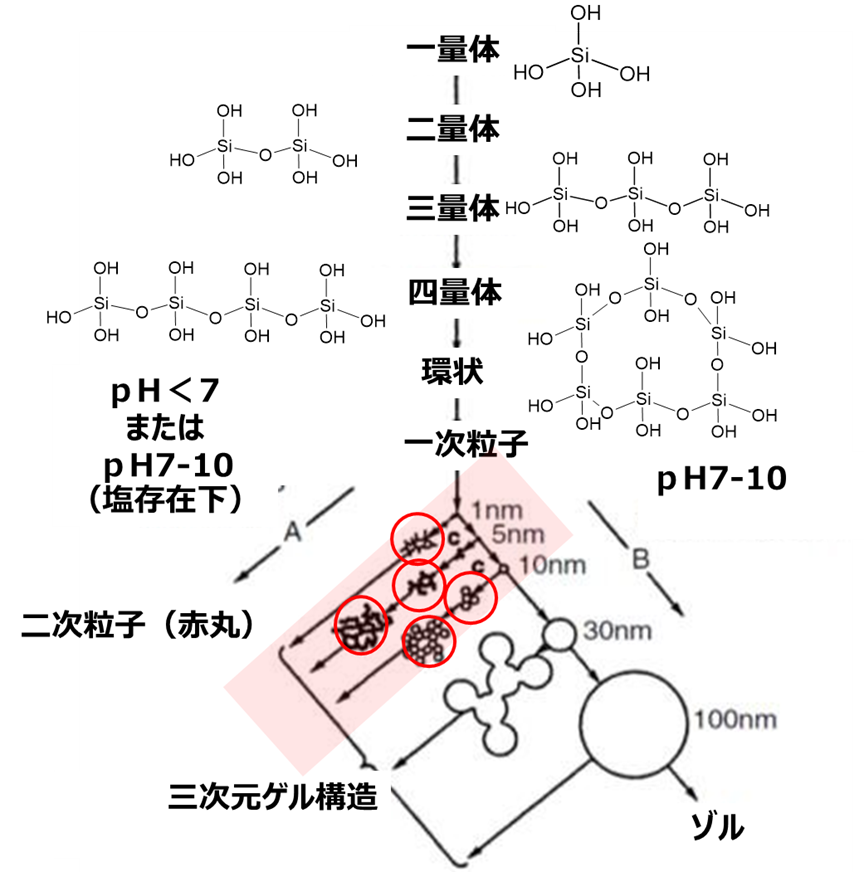
Fig3. 一次粒子から二次粒子の形成過程1)
粒子の特徴
Fig3に示したように、フュームドシリカの一次粒子は数nmから数十nm非常に小さく、この一次粒子どうしが数珠状にくっついてナノサイズの二次粒子を形成しています。
一般に物質は、粒子径が小さくなるほど表面積が増加するため粒子同士が引き合う力(凝集力)が大きくなり、粒子径が30µmより小さくなるとその効果は急激に大きくなります2)。
フュームドシリカの表面はシラノール基に覆われているため、シラノール基同士の水素結合により凝集力は更に大きくなります。
水素結合
水素結合(hydrogen bond)とは、OHやNHなど電気陰性度の高い原子に共有結合した水素原子が、近傍の他の官能基の非共有電子対と非共有結合的に作る結合です。
Fig4に示すように、水はOとHで引き合い水素結合が形成され、同じ現象がシラノール(Si-OH)基でも起こります。

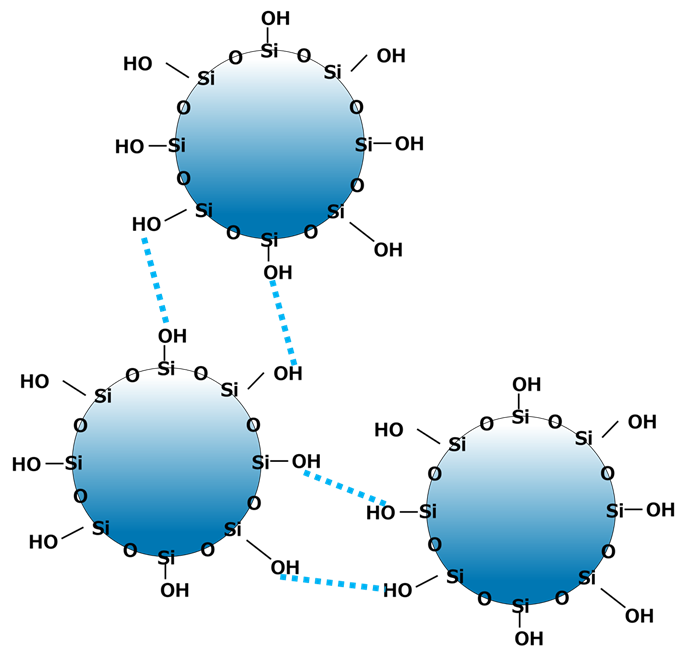
Fig4. 水およびシリカ粒子の水素結合
青い破線が水素結合を示す。
水やアルコールが同じような分子量をもつ化合物に比べて高い沸点を示すのは,分子間に水素結合を生じることが大きく寄与してるためです。たとえば、水(分子量18)の沸点が100℃であるのに対し、水素結合しないメタン(分子量16)の沸点はずっと低く、−162℃です。
水素結合の強さは10〜40 kJ/molの間であり、これは、ファンデルワールス力(1 kJ/mol程度)よりは強いが、共有結合(500 kJ/mol程度)弱く適度な強さを有しています。このため、室温で可逆的な結合・解離が可能となります。
また、生体分子の中で水素結合はとくに重要な働きをしていて、DNAやタンパク質などの生体高分子が機能的な高次構造を形成するのには、水素結合が欠かせません3)。
共有電子対と非共有電子対
水素結合は、非共有電子対同士の結合です。
一般にHやOをはじめとする非金属の原子同士は,不対電子を出し合って共有電子対をつくることにより結合して互いに安定な電子配置を取ります。この結合を共有結合といい,共有結合によってできた粒子を分子といいます。このとき、電子式の1対の共有電対を1本の価標で示した化学式が構造式となります。
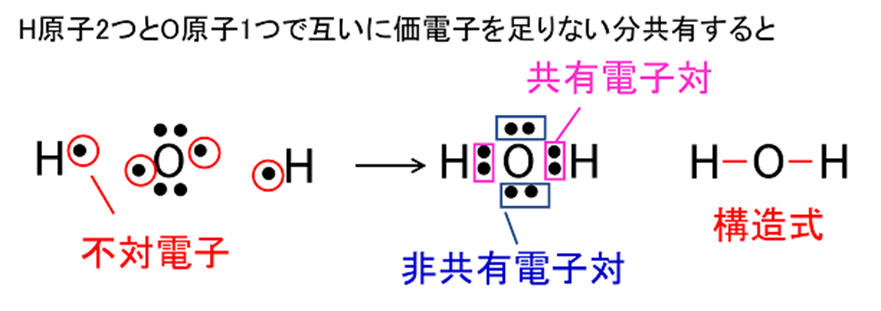
Fig5. 共有電子対、非共有電子対4)
粒子構造
フュームドシリカは、他の非晶質シリカに比べて一次粒子が小さくかつ二次粒子も小さく、かつシラノール基を有しているため水素結合も大きく、このため凝集性が非常に高い粒子です。 フュームドシリカの一次粒子は数nmから数十nm非常に小さく、この一次粒子どうしが数珠状にくっついてナノサイズの二次粒子を形成しています。したがって、二次粒子の凝集力も大きく、電子顕微鏡で観察した場合、シリカゲルのような一次粒子の凝集体のように見えますが、実際は二次粒子が集まって更に凝集体を形成するというのが特徴になります(Fig6)。
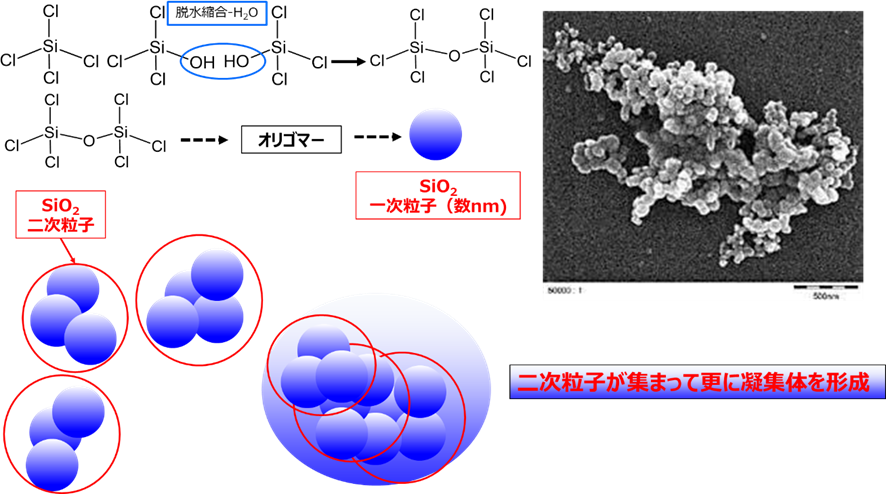
Fig6. 粒子構造のイメージと電子顕微鏡写真5)
この凝集は水の中ではより顕著に現れます。このため、正確な粒子径を測定するためには超音波等で強いシェアをかけて分散させる必要があります。
筆者の経験では、200nm程度のフュームドシリカを測定する際に30分以上高出力で超音波をかける必要があり、そのままではやけどをしてしまうほど温度が上がってしまう恐れがあったため、氷で冷やしながら行った経験があります。
このようにフュームドシリカは凝集力が強く少量で液体を増粘できるため、増粘剤としても広く用いられています。
フュームドシリカの製法
フュームドシリカは、主に火炎加水分解法で製造されています。火炎加水分解法とは、シリカ原として四塩化ケイ素を用い、1000℃程度の高温バーナー中で反応させてフュームドシリカを得る方法です。
反応を化学式で表すと、四塩化ケイ素が水素と酸素により加水分解されてシリカ単量体(SiO2)が生成します(Fig7)。この生成したシリカ単量体は、実際はFig6のように脱塩され、オリゴマーを経て一次粒子が形成されフュームドシリカになります。火炎加水分解工程で得られたフュームドシリカには塩酸が大量に含まれているため、その後の脱酸工程で塩酸を除去して製品となります。また、粒度や比表面積等の物性は加水分解反応時の反応条件を変えることでコントロールできます。更に、バーナーの代わりにアーク放電やプラズマを用いる反応法もありますが、基本的原理は変わりません。
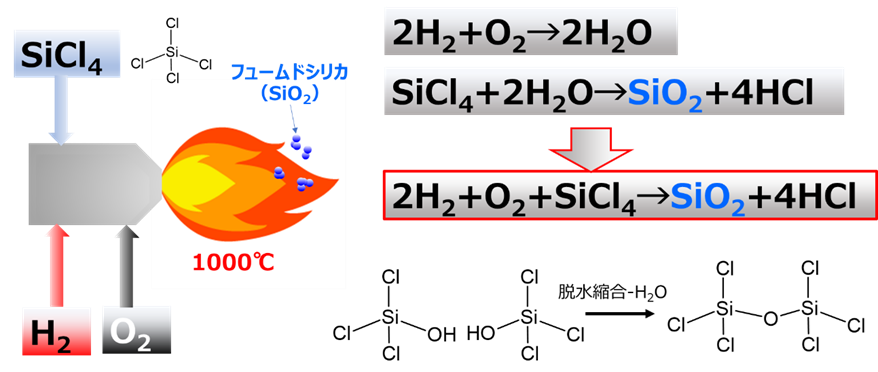
工業的製法
工業的にフュームドシリカは、四塩化ケイ素を加熱して酸素と混合し、その後バーナーで水素とともに燃焼させて、反応物を冷却させます。このとき冷却物にはシリカと塩酸(HCl)が混合しているため、分離器でHClを分離します。この状態ではシリカにHClが残存しているため、脱酸工程でシリカからHCl除去することで、フュームドシリカが得られます。
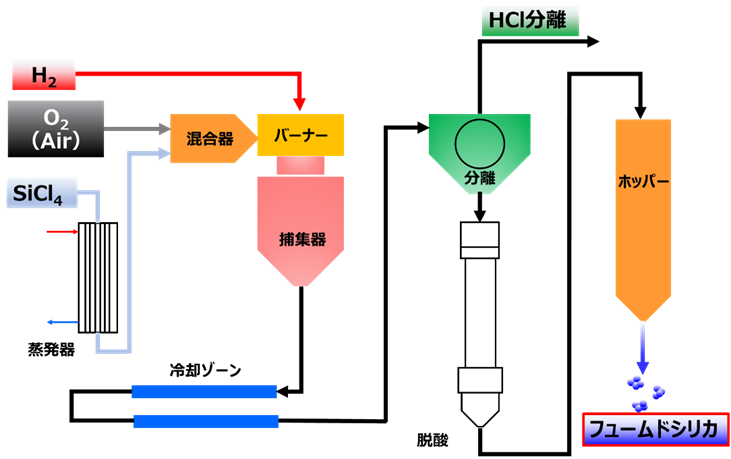
Fig8. フュームドシリカの工業的製法6)
半導体材料との関係
フュームドシリカの原料として四塩化ケイ素が用いられます。
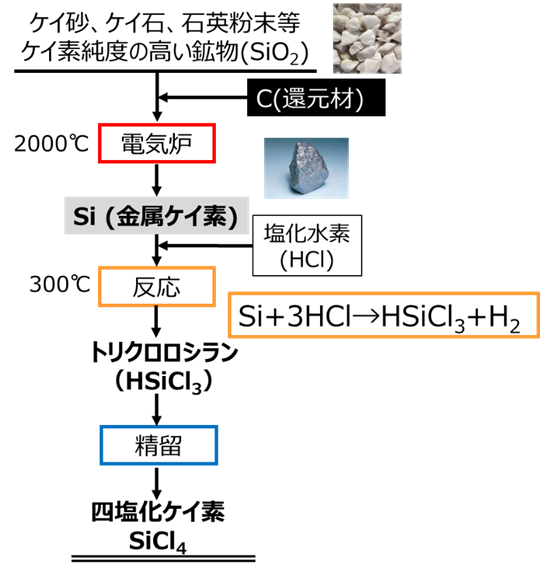
Fig9. 四塩化ケイ素の製法
Fig9のように四塩化ケイ素は、ケイ砂、ケイ石、石英粉末等の比較的ケイ素純度の高い鉱物に還元剤として炭素を加えて電気炉内で2000℃にて還元焼成をすることにより、Si(金属ケイ素)が得られます。この金属ケイ素に塩化水素を加えて300℃で反応させることで、トリクロロシランが得られ、ほとんどが半導体用高純度シリコンおよびシランカップリング剤の製造をするための原料に用いられています。
半導体の高純度シリコンは、を蒸留によって高純度に精製した後、約1000℃ の 温度下でCVD (Chemical Vapor Deposition)法 でを用い高純度多結晶シリコンを析出させます。
このときの反応は次のようになります。
4HSiCl3→Si+3SiCl4+2H2
この方法によって副生する四塩化ケイ素は、乾式シリカ(フュームドシリカ)の 製造原料として使用されます。
なお、高純度単結晶シリコンは、上記方法によって製造された多結晶シリコンを再度溶融した後、引き上げ法によって製造されています。
物理的性質
現在、工業的に生産されているフュームドシリカは、平均一次粒子径が7〜40nmでその比表面積は50~380m2/g 範囲の物性を有しています。そのうち50m2/gから200m2/gまでのグレードは、球形の一次粒子からなっているが、300m2/gのグレードになると、その表面は“しわ状”または“粗面”になっているといわれています7)。
平均一次粒子径
一般的に粉体の平均粒子径の測定には、対象物の性質により重量平均、個数平均、表面積平均、体積平均の4つの方法が用いられます。
前述しまたようにフュームドシリカは非常に凝集しやすい粒子であることから、正確な平均粒子径を測定するには、電子顕微鏡による測定が行われます。
このとき平均粒子径を算出する方法として、個数平均(dn)と表面積平均(da)がよく用いられます。
個数平均(dn)
電子顕微鏡で測定した粒子直径をその個数をもとに頻度をカウントする方法で、以下の式で表されます。
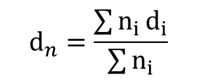
dn:個数平均 d:粒子直径 n:粒子個数
表面積平均(da)
別名体面積平均とも言われています。粒子の体積に対し、粒子表面積をもとに頻度カウントをする方法で、電子顕微鏡で測定した粒子直径から粒子を1個と数えるのではなく、その面積で頻度をカウントします。
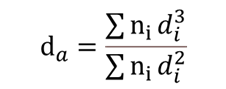
da:表面積平均
顕微鏡測定では、直径をどこで取るかが重要になってきます。Fig10に示すように真球でない直径がAとBと異なる粒子がある場合、個数分布ではどちらを取るかで大きく異なります。表面積平均は体積と表面積から算出されるためこのばらつきを抑えることが可能です。。
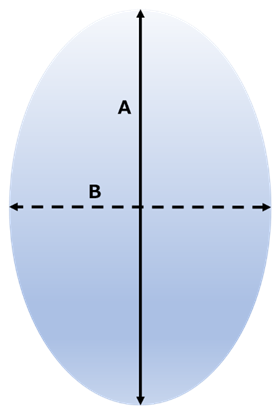
Fig10. 粒子径のイメージ
実際、粒子はさまざまな形状のものが存在するため、顕微鏡で粒子を測定する場合は、Fig11 に示す方法が定義されていて、これらを組み合わせて粒子径を算出します。
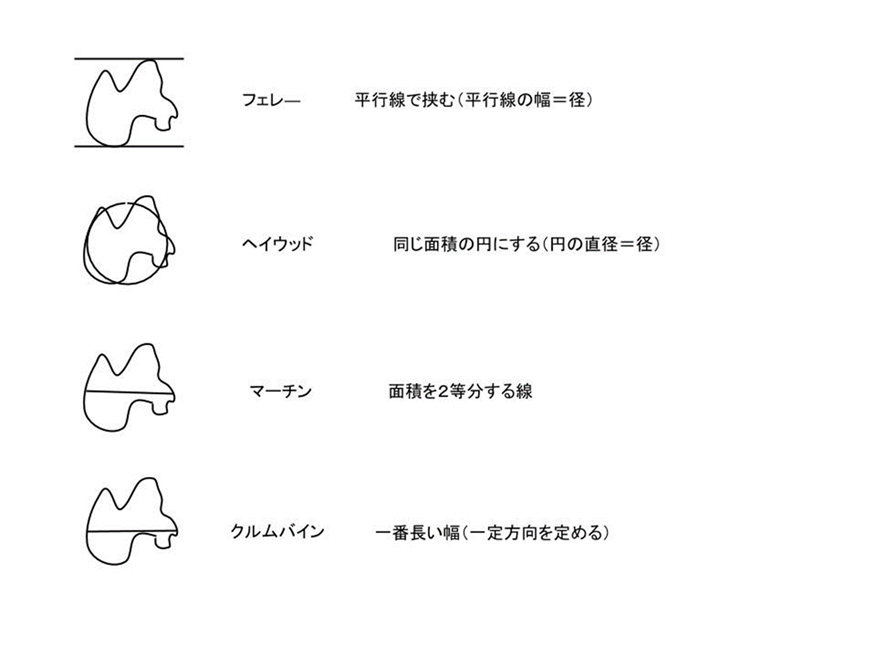
Fig11. 粒子径の定義8)
比表面積
フュームドシリカの比表面積(m2/g)はBET法により測定されるのが一般的です。
BET法とは、ある条件下において、粒子を低温状態にした時に粒子表面に物理吸着したガス量を測定し、比表面積を計算する方法で、Brunauer、Emmett、Teller の 3 名の頭文字をとってBET 法と名づけられました。
以下のリンク先でわかりやすく説明をされていますので、興味がありましたら参照してください。
https://www.an.shimadzu.co.jp/powder/lecture/middle/m02.htm
合成シリカとBETは切っても切れない重要な関係なので、詳細については後日、別の記事で説明をさせていただきたいと思います。
一次粒子径と比表面積の関係
フュームドシリカは、一次粒子径と比表面積から、Table1に示すようにA、B、C、D、4つに大別されます。
例えば、最も大きいものタイプAの一次粒子径は個数平均40nm、表面積平均60nmで一般に個数平均に比べて表面積平均の方が大きくなる傾向があります。また、90%スパンというのは、全体の9割に入る粒子径の大きさで、タイプAの場合、10~80nmの大きさを持った粒子が9割存在するということになります。この値は、粒子径が小さくなるほど狭くなり、最も粒子径が小さいタイプDの場合、一次粒子径が、個数平均では8nm、表面積平均では11nmで90%スパンでは5~13nmと非常に分布がシャープとなります。
Table1. フュームドシリカの一次粒子径の比表面積の関係9)

また、比表面積については、BET法による表面積と電子顕微鏡写真から求められた表面積がほぼ一致することから内部表面積を持たないということになります。
Fig12 のようにフュームドシリカは、一次粒子が数珠状に繋がっているため内部表面積はありません。
一方シリカゲルや沈降性シリカのような湿式シリカは一次粒子径の凝集により3次元構造が形成されていて、内部表面積が存在します。この傾向はシリカゲルが最も顕著です。
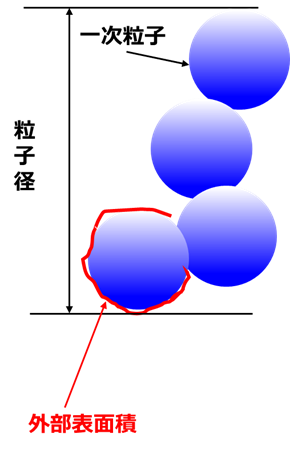
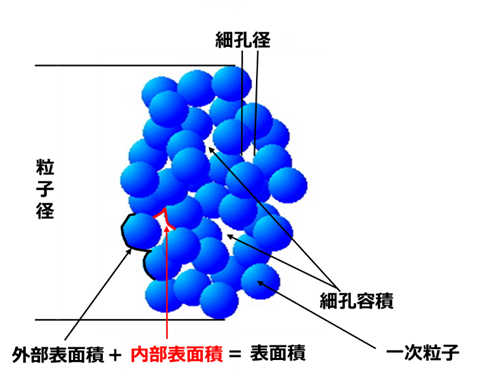
Fig12. フュームドシリカとシリカゲルの粒子構造
フュームドシリカの工業的基本物性
沈降性シリカ、微粉末タイプのシリカゲル、フュームドシリカは、別名合成粉末シリカといい、これらは工業材料としてさまざまな分野に用いられています。
Table2に合成シリカの工業材料として要求される基本物性を示します。
Table2. 合成粉末シリカの工業的に要求される基本物性10)
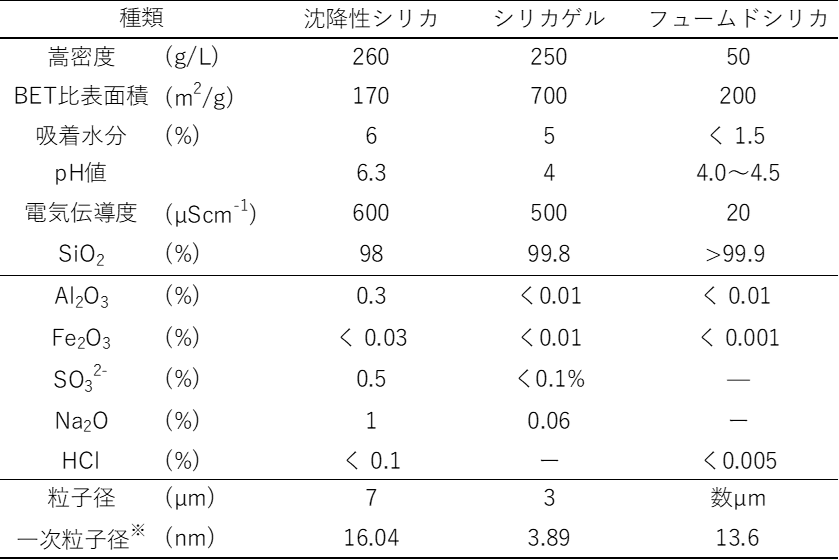
※一次粒子径は計算により算出
比表面積と一次粒子径の関係
シリカゲルの内、比較的に高い比表面積を持つグレードの比表面積は700(m2/g)程度で、沈降性シリカやフュームドシリカの約3.5~4倍程度高いものとなります。これは、先に示したシリカゲルの構造によるもので、内部表面積の有無が関係しています。
Table1では、電子顕微鏡を用いた一次粒子径の算出方法をお示ししましたが、一次粒子径は次の方法で比表面積から簡単に求められ、電子顕微鏡による方法と近い値が得られます。
一次粒子径を球状粒子として仮定して、このとき粒子径をd、密度をρとします。
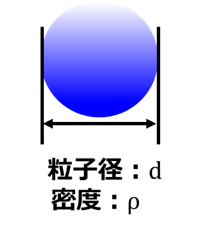
一次粒子一個の体積は次ようになります。
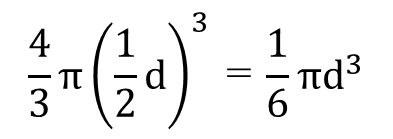
このとき、粒子1個の表面積は次のようになります。
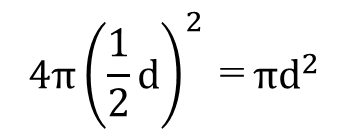
一次粒子1個の重量は、体積×密度で次のようになります。
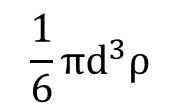
一次粒子を、真球状で細孔の無い粒子と仮定したとき、以下の式が成り立ちます。
比表面積:S=一次粒子を1g集めたときの表面積(内部+外部)の総和


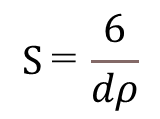
一次粒子の粒子径dとすると
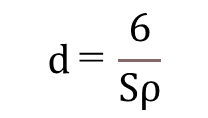
使用する単位はd: nm、ρ: g/cm3、S: m2/g なので単位を合わせると。

よって、一次粒子の大きさは、比表面積と密度(比重)がわかれば一次粒子径の大きさは求められます。
更に、シリカの真比重(ρ)は2.2(g/cm3)のため、比表面積S(m2/g)がわかれば簡単に一次粒子径が求められます。
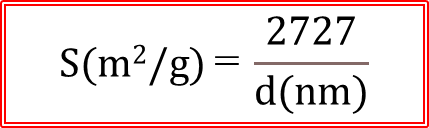
電子顕微鏡で算出したフュームドシリカ(C)の平均粒子径は、個数平均で9nm、表面積平均で14nm、90%スパンでは5~15nmを取ります。
一方、計算による値は、13.6nmから、電子顕微鏡の算出値にほぼ一致しているものといえます。
更にこの方法で、沈降性シリカやシリカゲルの一次粒子径も算出したところ、それぞれ16.04nm、3.89nmとなり、シリカゲルは比較的小さな一次粒子径で構成されていて、内部比表面積も有するため表面積が高くなることがわかります。
また、嵩密度についてフュームドシリカは、一次粒子が数珠状に繋がり緩やかな凝集体を形成している構造を取っていることから、1L当たり50gと嵩密度は最も小さくなります。
不純物
Al2O3、Fe2O3、SO32-、Na2O、HClは、製品のシリカ(SiO2)に含まれる不純物で、合成粉末シリカの製法に大きく関係しています。
Fig3に合成粉末シリカの製造フロー図を示します。
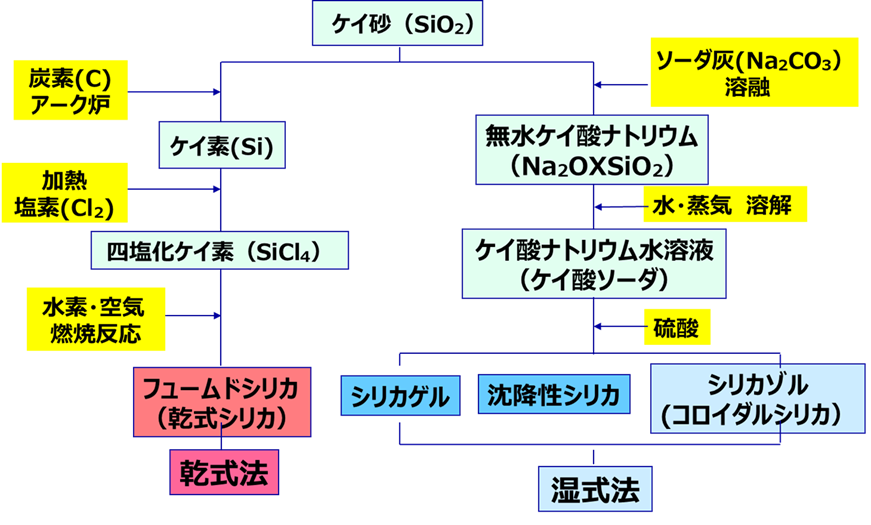
Fig13. 合成粉末シリカの製造フロー
フュームドシリカは先にも述べたように、四塩化ケイ素に水素と空気(酸素)を加えて反応させて乾式法で製造するため、金属不純物量は非常に少ないものとなる反面、副産物として塩酸が生成するため、若干ではありますが、塩酸が残存しています。
一方、沈降性シリカやシリカゲルはケイ酸ソーダに硫酸を加えて製造されるため、ケイ酸ソーダ由来の金属不純物が高くなるとともに、硫酸からの硫酸根(SO32-)が残存しています。
シリカゲルの場合は、反応により比較的大きな粒子を得た後、水洗により金属不純物や硫酸根を除去した後に粒度調整を行い製品となりますが、沈降性シリカの場合、反応により形成される粒子が非常に小さいため、水洗により金属不純物や硫酸根をシリカゲルに比べ除去し難く、更に粒子骨格も不安定というのが原因となります。
また、塩酸の残存は反応調整として塩酸を加えているからと考えられます。
このように、フュームドシリカは他の合成粉末シリカに比べ金属不純物量が非常に少ないのが最大の特徴となります。
金属不純物や残存する酸量は、合成粉末シリカの製法と密接に関係していて、ここから種類や製法の推察も可能です。
主な用途
フュームドシリカの用途は以下のように4つに大別されます。
液体製品の増粘とチキソトロピー性の付与
フュームドシリカを液体製品に添加すると、シリカ表面のシラノ ール基が互いに水素結合することにより液体中で三次元の網目構造を形成します(Fig14)。
その結果、液体の粘度は高くなり、チキソトロピー性も付与することができ、製品中の顔料やフィラーの沈降が防止できます。
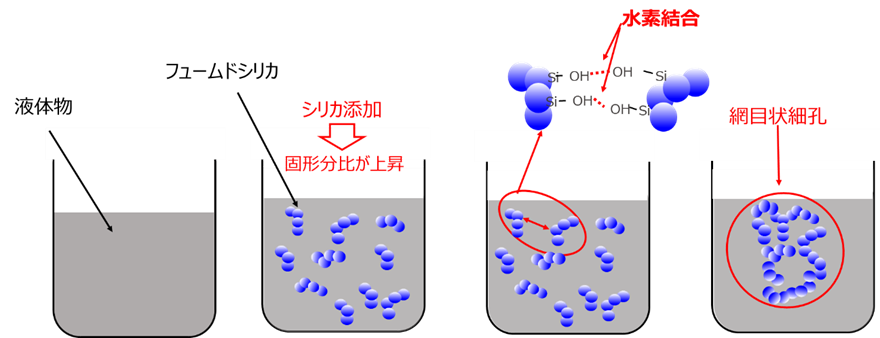
Fig14. フュームドシリカによる増粘のイメージ
チキソトロピー性とは、日本語では揺変性(ようへんせい)といいます。
Fig15にチキソトロピー性液体の粘度―時間線図を示します。
せん断力をかけない状態では粘度が高く一見固体のように見えるのに、かき混ぜたり振ったりするなどのせん断応力を与え続けると粘度が低下して液状になり、応力を除くと徐々に粘度が回復して元に戻るという性質がチキソトロピー性です。
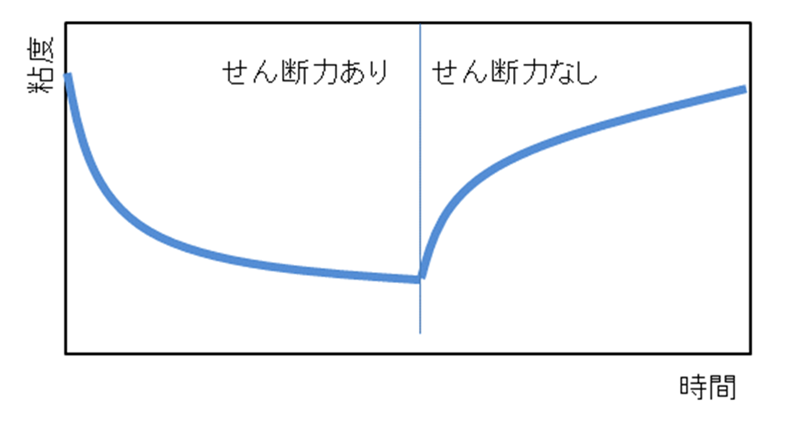
Fig15. チキソトロピー性液体の粘度―時間線図11)
例えば塗料は、かき混ぜて塗るときには粘度が低くて作業性が良好で、壁に塗った後はすぐに粘度が上がって下に流れないように工夫されています。これは、チキソトロピーの性質を持たせているからで、フュームドシリカが重要な役割を果たしています。
Fig16に示すように、フュームドシリカは疎水、親水性問わずさまざまなものに対して増粘効果を付与でき、更に添加量によりコントロールができるため、さまざまな製品の増粘やチキソトロピー性付与に使用されています。
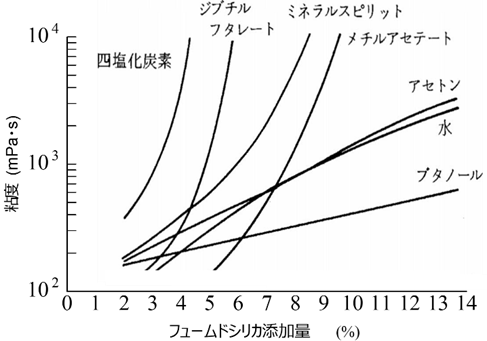
Fig16. フュームドシリカの添加量と粘度の関係12)
ゴムなどエラストマーの補強充填剤
補強充填剤用途として、合成ゴムやシリコーンゴム、シーラントなどに使用されています。
一般にゴムなどの補強には過酸化物による架橋が一般的です。しかし、熱加硫型(HTV)シリコーンゴムや室温硬化型(RTV)および液状シリコーン(LIM)は架橋しても強度が上がらないため、フュームドシリが用いられていて、ポリマーに対して20から30パーツ混練することにより、約40倍強度が向上することが報告されています13)。
また、これらのポリマーに使用するフュームドシリカは、表面処理を行ったものが使用される場合もあります。
粉体製品の固結防止、流動性改善剤
フュームドシリカは、ナノサイズの超微粒子が凝集してミクロンサイズの空隙を形成しているため、その空隙に水分を保持することができます(Fig17)。
また、ナノサイズの超微粒子のため少量で対象物をコーティングできます。
このため、粉体塗料、粉末消火剤、乾式コピー機のトナーにも用いられています。
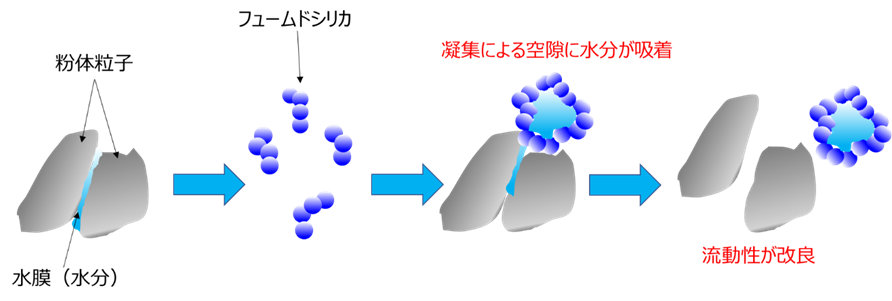
Fig17. フュームドシリカによる流動性改良のイメージ
超微粒子、高純度、断熱性、吸着作用の利用
フュームドシリカは、金属不純物を含まず、超微粒子で粒子間空隙による吸着性能も有しています。
このため、石英ガラス製造原料、ジアゾ感光紙のコントラスト改善、繊維のすべり性向上,シリコンウヱハーの研磨材、トレーシングペーパーーのつや消し、耐火物の強度向上、触媒の担体、セメントの強度向上、ポリエチレンバッテリーセパレーターの微細孔の形成、蛍光体顔料の合成原料、PPやPEフィルムのブロッキング防止、IC封止材用フィラーの合成原料などにも用いられています14)。
まとめ
フュームドシリカは四塩化ケイ素を原料として製造され、数nmの一次粒子が数珠状に繋がって二次粒子を形成しているのが特徴の一つです。
合成粉末シリカの中で最も小さくナノサイズの粒子径のため粒子同士の凝集力が非常に強く、さまざまな材料の増粘剤として用いられています。更に、その凝集より形成された粒子間隙に水をはじめさまざまな液体を吸収できることから、流動性改良剤、各種担体にも用いられています。
フュームドシリカの一次粒子径は電子顕微鏡による粒子径の測定で求められますが、すべてを球状粒子として仮定した場合、BET法による比表面積の値と真比重の値から簡単に求めることができ、その結果は、電子顕微鏡による測定値と近い値となります。
参考文献
1) R.K.ILER, The Chemistry of Silica ,p174 をもとに筆者加筆
2) 神保元二 粉体の科学―最先端技術を支える「粉」と「粒」 (ブルーバックス (B‐613))講談社1985 p21
3) 第2章 生命の化学的基礎 https://www.tmd.ac.jp/artsci/biol/pdf3/Chapt2.pdf p15
4) 3 分子と共有結合 https://pigboat-don-guri131.ssl-lolipop.jp/313%20Molecule%20%20and%20covalent%20bond.html
5) 藤野 秀幸 J. Jpn. Soc. Colour Mater., 88〔8〕,pp. 279–281(2015)
6) ナノマテリアル情報提供シート 日本アエロジル株式会社 経済産業省 p11を参考に作成
7) 落合 満 エアロゾル研究 Vol.5 No.1 (1990) p33
8) 粉体の性質 https://yaku-tik.com/yakugaku/sz-1-3-4/
9) 落合 満 エアロゾル研究 Vol.5 No.1 (1990) p34
10) 落合 満 エアロゾル研究 Vol.5 No.1 (1990) p34をもとに筆者作成
11) 株式会社タイカ https://taica.co.jp/gel/support/technical_terms/term_041.html
12) AEROSILカタログNo.12 (日本アエロジル社) (1989)
13) 落合、前掲論文 p40
14) 落合、前掲論文p42
コメント
コメント一覧 (1件)
[…] 乾燥剤(シリカゲル)詳細につきましては、フュームドシリカ、シリカゲル、沈降性シリカの各解説記事をご覧ください。 […]