As you all know, silica is used not only in automobiles, but also in bicycles, motorcycles, airplanes, and trains, and is indispensable in everyone’s lives. In fact, fine silica is also used in tires, and is indispensable for the eco-friendly tire technology that has been attracting attention recently. In this article, we will explain about tires and silica.
Manufacturing Process of Tires
Generally, tires are manufactured in six steps: (1) kneading, (2) part preparation, (3) molding (assembly of parts), * (4) vulcanization (attaching patterns and markings), (5) inspection, and (6) shipping.
Silica is used in the kneading process. Silica (fine silica particles) is mixed with carbon black, sulfur, and compounding agents with natural and synthetic rubber as the base material, then processed into sheets and sent to the next process.
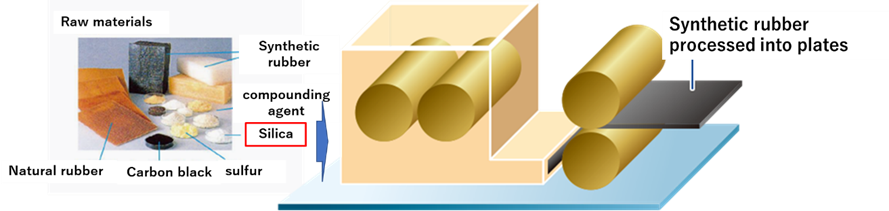
Fig1. Tire raw materials and blending process
The raw material mix depends on the type of tire and its performance! Rubber processed into sheets is the source for making each part.
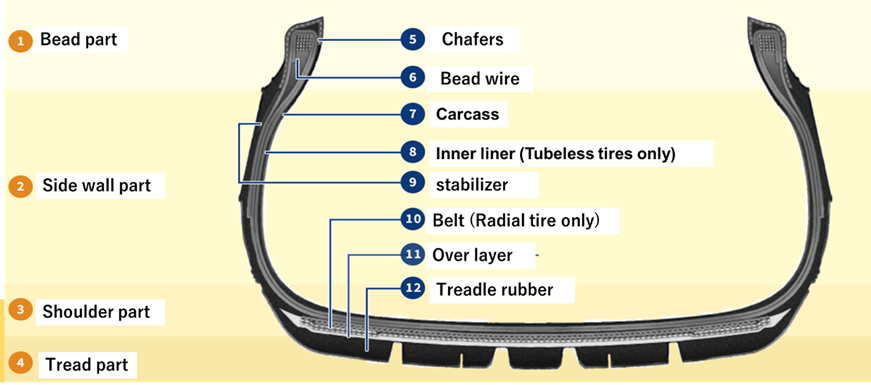
Fig2. Tire Composition and Parts1)
Each part is divided into three parts: “tread part,” “carcass part,” and “bead wire part.
Each part is completed through the processes of cutting, pasting, and coating.
The vulcanization process is different from the vulcanization process described in the next section, as it is the process of attaching patterns and stamps to tires.
Role of Silica
For tires, silica is a reinforcing material for rubber, and is known as white carbon as opposed to carbon powder (carbon black). Fine silica particles are indispensable to enhance the wet performance of tires, and the key point is how to evenly mix a large amount of good quality silica in the compound.
Many tire manufacturers have developed tires that use silica, and Yokohama Tire has developed a “kneading” technology that allows a larger amount of silica to be dispersed evenly in the rubber in a smaller diameter, as a result of repeated research and analysis over the past 20 years.2)
The key point is how to disperse a large amount of fine silica particles in this tire rubber, and each tire manufacturer is conducting research and development.
Effect of Silica Addition
The effect of silica addition is to improve fuel efficiency and grip performance on wet road surfaces.
Fuel Economy Improvement
The addition of silica speeds up tire recovery from deformation compared to non-additives, and tires that have been deformed by uneven road surfaces quickly return to their original shape (a perfect circle), resulting in less rolling resistance. Furthermore, the generation of frictional heat is reduced compared to carbon black. For these reasons, silica is used in many eco-friendly tires in recent years because it reduces fuel consumption compared to conventional tires.
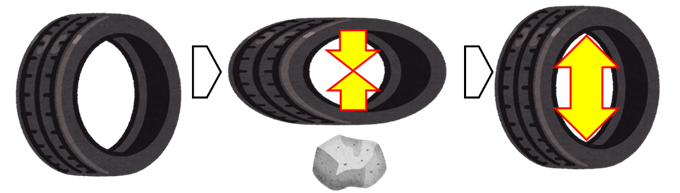
Fig3. Image of reduced rolling resistance
Improved Grip Performance
Grip performance of a tire is the ability of the tire to hold the road surface during driving. Grip performance can be divided into dry grip performance on dry surfaces with high frictional resistance and wet grip performance on wet surfaces with low frictional resistance. Silica plays a role in improving the wet-grip performance of tires.
Wet-Grip Performance
Wet grip performance and adhesion friction are closely related, and silica contributes to improving tire adhesion friction.
Friction Formed by Adhesion
Adhesion friction is the friction that occurs when an object is pressed against an installed surface. Since tires are always installed and used with road surfaces, it is one of the most important evaluation indicators for tire performance. Road surfaces are always microscopically uneven. As the tire rotates over these bumps, the rubber on the ground (tread) is slapped against the bumps. At this time, there is a recoil from the slamming and a grip generated when the rubber is pulled away from the road surface. This grip is adhesion friction, and the mechanism is similar to the rotation of gears.
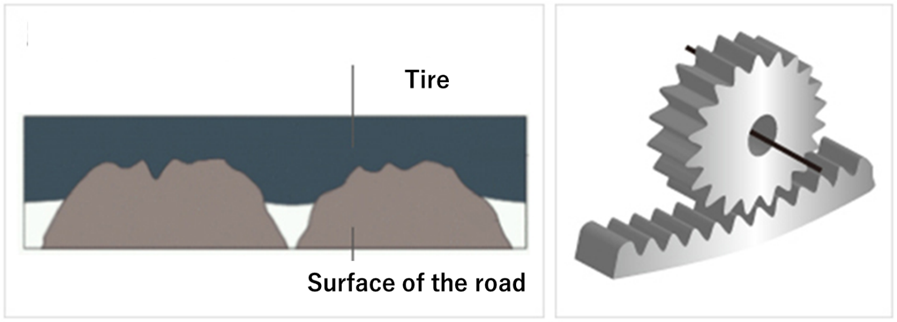
Fig4. Image and gear of ground contact3)
Effect of Silica Addition
Pre-molded tire rubber (compound) with silica improves the ability to follow the micro-unevenness of the road surface, and as a result, improves wet grip. On the other hand, a moderate balance is necessary, because the more silica is added to the compound, the harder it becomes, which increases the heat generation of the tire, thereby worsening its rolling resistance.
Silica improves the viscosity of the compound. There are two mechanisms to improve viscosity.
The other is the attraction (hydrogen bonding) between silica and silanol groups. The strength of hydrogen bonding is between 10 and 40 kJ/mol, which is stronger than van der Waals force (about 1 kJ/mol) but weaker than covalent bonding (about 500 kJ/mol), enabling reversible bonding and dissociation at room temperature.
Since thickening by silica can be easily controlled by the amount added, it is used as a viscosity adjuster in many fields, including tires, paints, plastics, and other industrial materials, as well as toothpastes, creams, and ointments, due to its high safety profile.
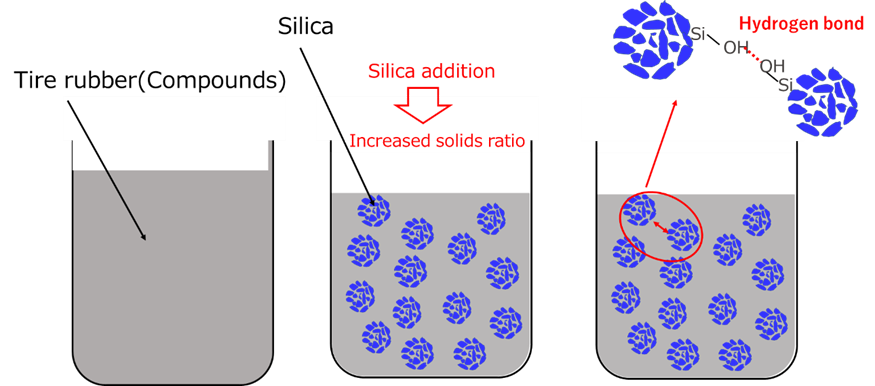
Fig5. Thickening mechanism of silica
Challenges of Silica Addition
Rubber and silica are difficult materials to disperse uniformly because of their water/oil relationship. Particularly for silica with small particle size, the dispersion technique is highly difficult, and agglomeration, or so-called silica lumps, are easily formed. Silica lumps are caused by hydrogen bonds between silanol groups (Si-OH) on the silica surface, and the bonds form agglomerations.
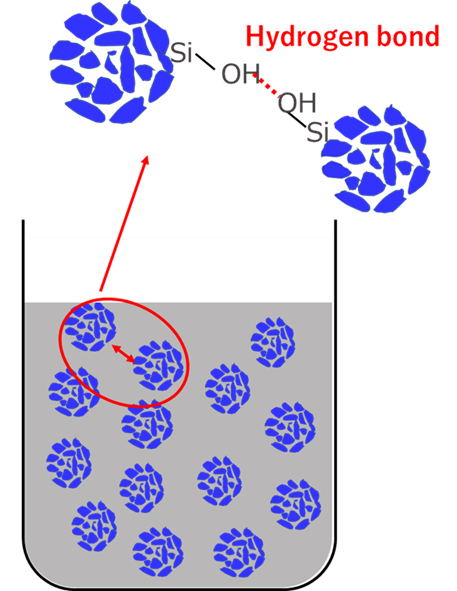
Fig6. Image of silica agglomeration
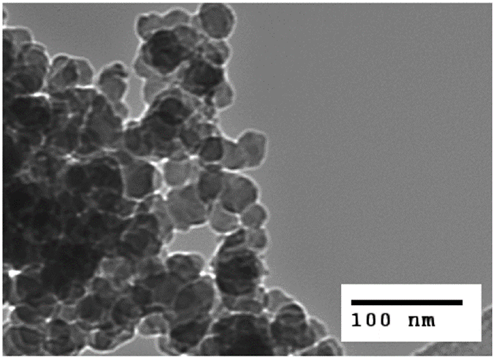
Photo1. TEM photograph of fine silica particles in rubber4)
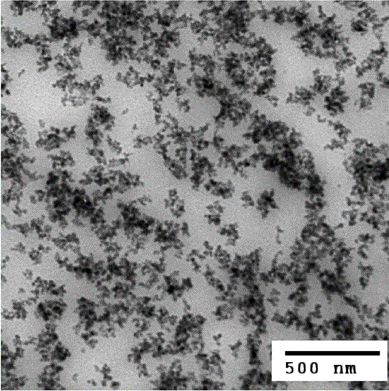
Photo2. Dispersion of silica (30 mass% content) in rubber (TEM observation image)4)
The problem was how to uniformly distribute silica in the tire at a high level, since these lumps rub against the rubber and generate heat, resulting in a loss of rolling resistance.
Methods to Reduce Agglomeration
Methods to suppress agglomeration can be broadly classified into surface treatment methods and additive methods.
Surface Treatment Method
This method replaces the H of silanol group (Si-OH) on the silica surface with other hydrophobic molecules and is called the surface treatment method, and the molecules to be replaced are called silane coupling agents.
Tires are treated in two steps: first, silica is dispersed in rubber by reacting with silane coupling agent and silica surface (dispersion reaction), and second, the polymer chain of tire rubber (polymer chain) is cross-linked by sulfur while the polymer chain and silica are linked and fixed through silane coupling (vulcanization reaction). The process is carried out in two stages.
The production of silane coupling agents is expensive, and the cross-linking agent is adsorbed on the silica surface, which affects the cross-linking.
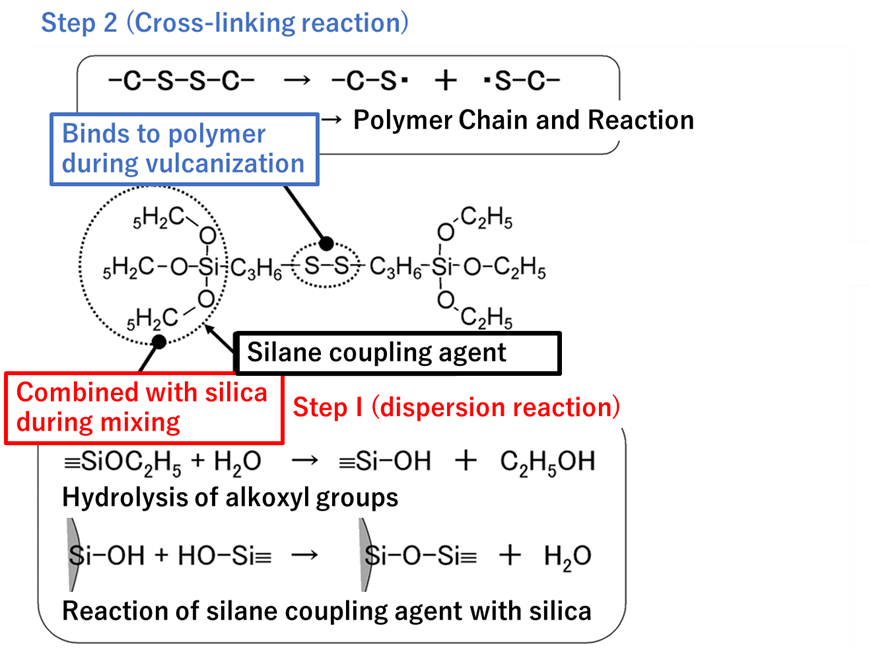
Fig7. Overview of dispersion and cross-linking reactions4)
Dispersion Reaction
During mixing, the OH generated at the end of the silane coupling, which is produced by hydrolysis of alkoxyl groups, reacts with the OH of the silanol groups through dehydration-condensation. At this time, the silica surface becomes partially hydrophobic, which gradually improves its compatibility with rubber, thus promoting dispersion. This reaction should take several minutes and is generally carried out at temperatures of 150°C or higher. Note that if the temperature is too high, the -S-S- bond is decomposed and the reaction between the silane coupling agent and the polymer occurs during kneading, resulting in a significant deterioration in processability.
In addition, since the dispersion of silica proceeds with the reaction, more precise process control is required.
Vulcanization Reaction
After the silica is thoroughly dispersed, a cross-linking agent is added and a vulcanization reaction takes place at 150-170°C. In the vulcanization reaction, the -S-S- bonds break down and the sulfur moiety covalently bonds to the polymer. During the vulcanization reaction, the -S-S- bonds are decomposed and the sulfur moiety is covalently bonded to the polymer. The resulting bond between silica and polymer via the silane coupling agent improves reinforcement and wear resistance.
The vulcanization reaction produces elasticity in rubber. Elasticity is one of the characteristics of rubber. Therefore, when it is deformed, it does not return to its original shape, and the distortion caused by the deformation remains.
On the other hand, vulcanized rubber has a three-dimensional network structure with cross-linking points formed between molecular chains through a chemical reaction. For this reason, when deformation is applied, the rubber only expands and contracts, but no distortion remains.
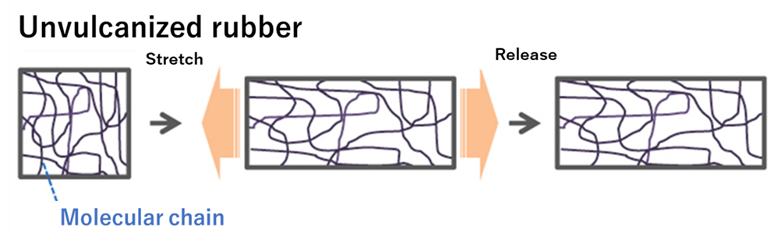
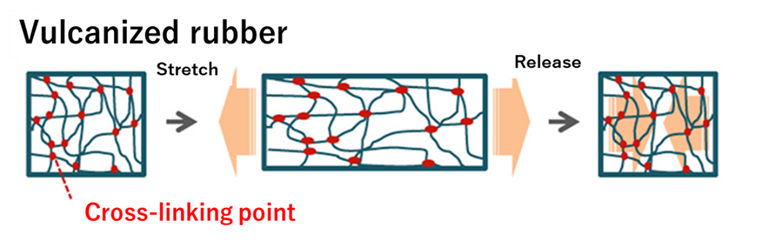
Fig8. Physical properties of unvulcanized and Vulcanized Rubber5)
Method of Addition
Silica is mixed with a dispersing agent and added to rubber. This method does not require a controlled silane coupling agent as in the surface treatment method and does not affect silica adsorption because silica is dispersed in the additive. On the other hand, it is necessary to consider the effect of the additive on the cross-linking process.
Recently, in November 2019, a patent jointly applied for by Kao Corporation and Bridgestone Corporation as an additive composition for silica blended rubber compositions, rubber compositions, and tires was granted6). This silica dispersant has higher dispersibility than conventional dispersants and, moreover, is mainly composed of glycerol fatty acid esters, which are 100% derived from plant materials, contributing to activities for the realization of a sustainable society!
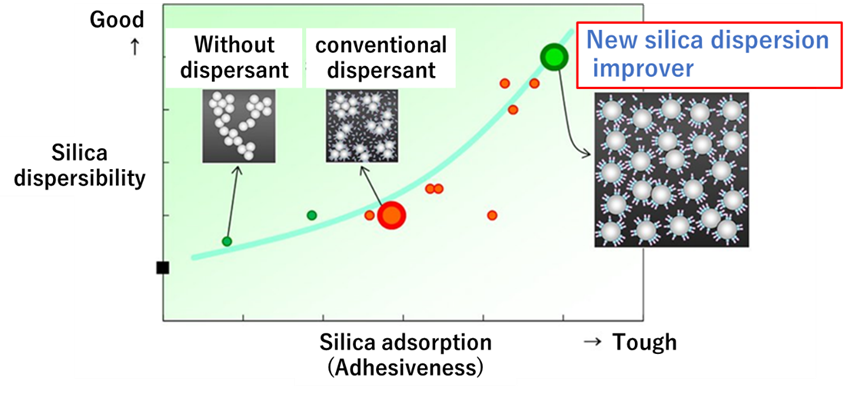
Fig9. Properties of the new silica dispersant7)
Glycerol fatty acid esters are esters of fatty acids attached to one or two of the three hydroxy groups of glycerin. A fatty acid ester bonded to one of the three hydroxy groups of glycerin is called a monoglyceride.
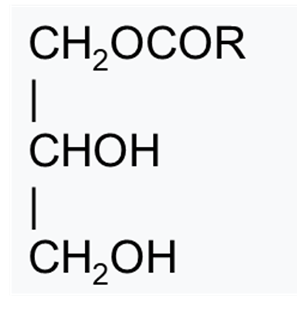
Structure of monoglycerides
Electrical Resistance of Tires
Silica, like glass, has high insulating properties, and the electrical resistance of silica-added rubber is 1016Ω, which is very high compared to the 10-5 to 10-6Ω electrical resistance of ordinary tires. The higher the value of this electrical resistance, the greater the insulating properties and the easier it is for static electricity to build up. Compared to tires without silica, tires with silica are more insulating and therefore less conductive, making it impossible for static electricity to be discharged from the vehicle to the ground. This is why there are concerns that sudden discharges of static electricity from silica-based tires can ignite combustible materials and adversely affect electronic equipment due to electromagnetic noise.
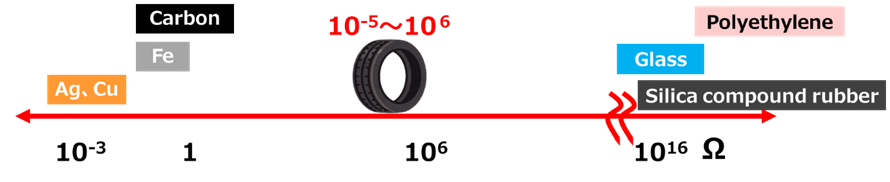
Fig10. Tires and other electrical resistance8)
To solve this problem, silica compound tires are equipped with a conductive slit, or ground, to dissipate static electricity generated by the vehicle to the ground.
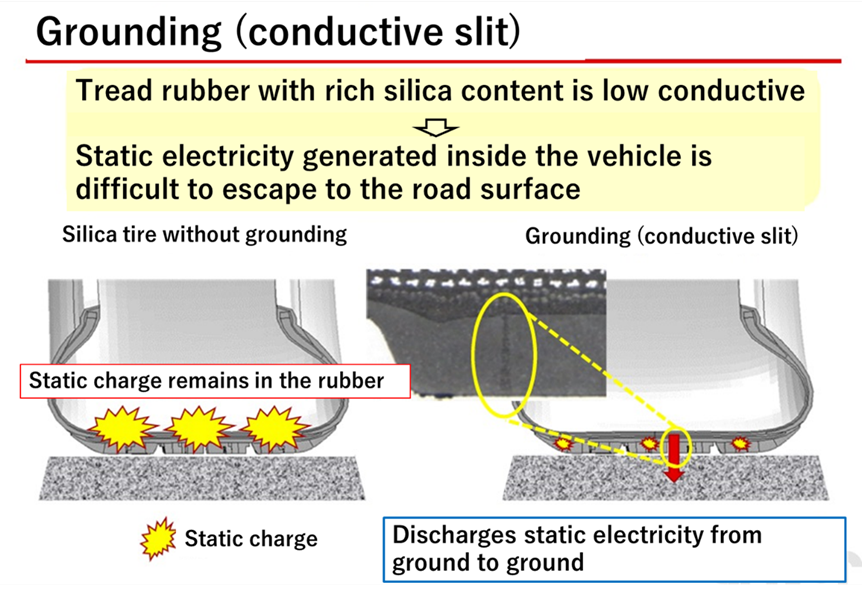
Fig11.Overview of Conductive Slits8)
Conclusion
When added to tires, silica improves fuel economy by reducing rolling resistance and improves wet grip performance. These effects are due to silica’s thickening properties, and silica is used as a viscosity modifier not only in tires, but also in paints, plastics, and other industrial materials, as well as in toothpastes, creams, ointments, and many other fields due to its high safety profile.
Silica used in tires must have fine particles and good dispersibility. Generally, the finer the particles, the greater the surface energy, making dispersion more difficult. For this reason, surface treatment and additive methods are used to improve the dispersibility of silica. These techniques are used not only for tires but also in other fields. For example, surface treatment techniques using silane coupling agents are also used for chromatographic silica (Fig12).
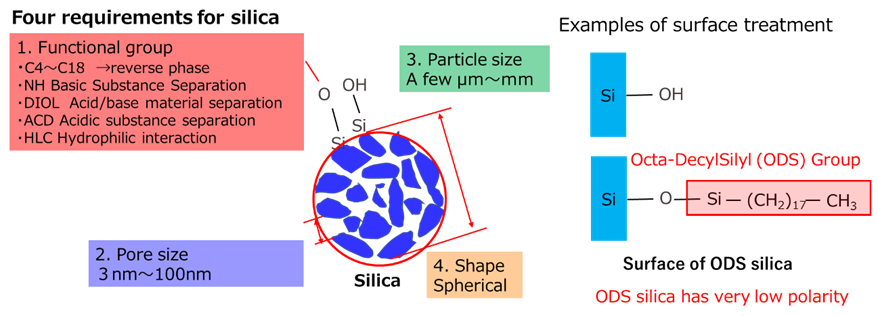
Fig12. Properties required for chromatographic silica
Silica is used in a variety of fields including clothing, food, and housing, so you may find a solution to your problem by searching for technology with the keyword “silica.
References
1) Good Year HP https://www.goodyear.co.jp/knowledge/production-method.html
2) ヨコハマタイヤ HP https://www.y-yokohama.com/about_yokohama/newsletter/no12/
3) グリップ(凝着摩擦)について | タイヤはピットイン (pit-in.co.jp) https://www.pit-in.co.jp/tire/
4) タイヤ材料におけるシリカナノコンポジット成形加工 Vol. 25 No. 3 2013
5)錦城護膜(株)HPより引用http://www.kinjogomu.jp/rubber/qa.html
6) 特許第6608652(2019/11/01登録)シリカ配合ゴム組成物用添加剤組成物、ゴム組成物及びタイヤ
8) CARVIEW! HP https://carview.yahoo.co.jp/news/detail/304862588c18dddec7d92c9e6aa6fb508d7d9a7c/photo/?page=3
コメント